Additive Manufacturing3D造形
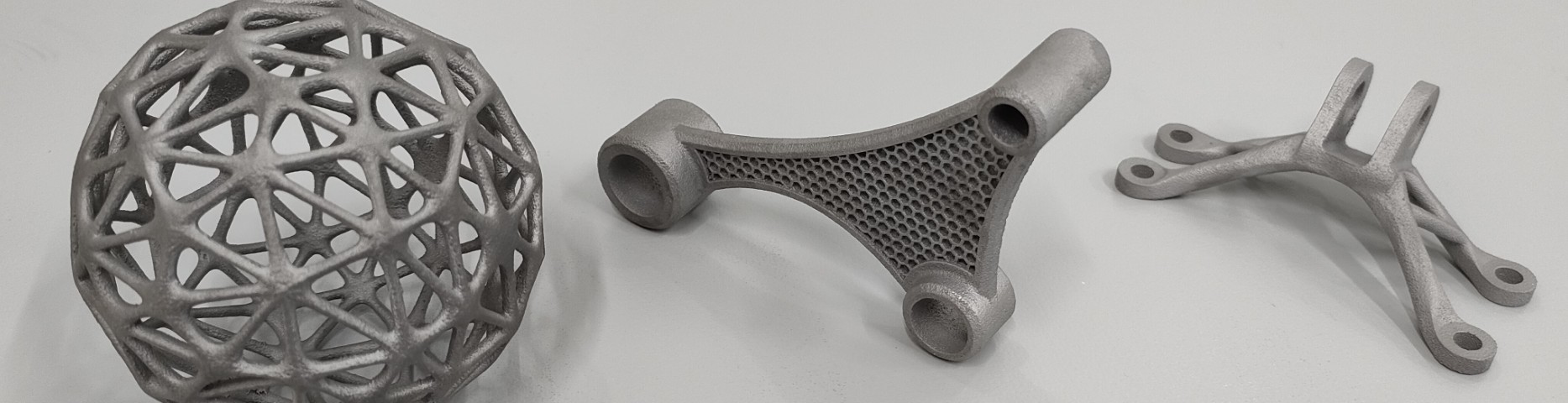
3D Printer3Dプリンター
金属3Dプリンター
型式 | LPM325/RM4RP |
---|---|
メーカー | ㈱ソディック |
最大造形寸法 | 250×250×250mm (ベースプレート含む) |
造形方式 | パウダーベッド方式 |
レーザー方式 | Ybファイバーレーザー(Max.500W) |
適用金属 | Alsi10Mg 、SUS630、64Ti |
樹脂3Dプリンター
型式 | Projet3500HDMax |
---|---|
メーカー | 3D Systems |
最大造形寸法 | W183×L298×H203mm |
造形方式 | インクジェット方式で紫外線硬化樹脂を一層ずつ積層 |
最小積層ピッチ | 0.016mm |
樹脂材料 | VisiJet® M3 Crystal (半透明) |
造形サンプル
-
ボリュートポンプ部品(AlSi10Mg) -
造形限界サンプル(AlSi10Mg) -
インペラ(AlSi10Mg)[ブラスト後]
What’s 3D Printing?3D造形とは
3D造形は、Additive Manufacturing[通称AM]と呼ばれる加工技術の一つで、3Dデータをもとにして、スライスされた2次元の金属粉末等の層を一層ずつ積み重ねていくことにより、3次元の造形物を製造するものです。3D造形では、機械加工等の従来加工法では実現が難しい3次元複雑形状品の加工が可能で、次世代の加工技術として注目されています。
(1) 形状の自由度が高い
複雑な形状の金属部品も造形することができます。また、従来は複数のパーツから組み立てていたものを、組み立て後の状態で造形し、組立工程を無くすということもできます。
構造最適化を組み合わせることで、今までは実現できなかった必要機能を維持したまま部品を軽量化することが可能になります。
(2) 試作やアイテム1個から手軽に造形可能3Dプリンター用のデータを用意するだけで新しいアイテムを造形できるため、開発コストをほとんどかけずに、簡単にアイテム数を増やすことが可能です。また、治具や型を用いないため、3Dデータを修正するだけで試作の結果を簡単にフィードバックすることが可能です。
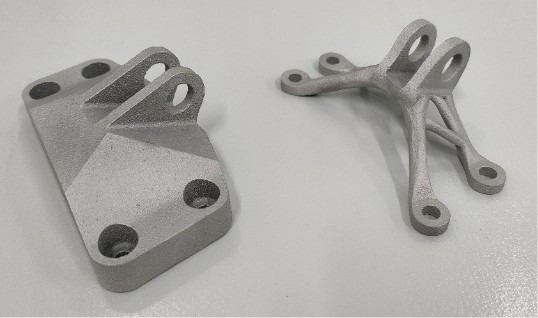
(左:最適化前、右:最適化後)
● デメリット
(1) 造形スピード
積層造形は、1層(0.04~0.05mm)ごとに材料を積み重ねて造形する仕組みのため、1つの製品を完成させるまでに時間がかかります。
そのため、鋳造や切削などの従来工法で早く製造可能な場合、その方法で加工する方がコストが安く済むことが多いです。
(2) 造形精度
光造形方式の樹脂3Dプリンターの場合は±0.05mm程度の精度で造形が可能ですが、金属3Dプリンターの場合は、
一般的に寸法精度:±0.2mm程度、面粗さ:Ra10~20程度となります。そのため、造形したままでは寸法や面粗さの厳しい金属製品に適用ができません。
弊社では、熱処理、機械加工を組み合わせることで、寸法精度や面粗さが必要な部品にも後加工で対応が可能です。
積層造形の原理
金属積層造形 – パウダーべッド方式(PBF:Powder Bed Fusion)
ベースプレートと呼ばれる金属土台の上に金属粉末を敷き、造形する部分にレーザや電子ビームを照射し溶融・凝固させ積層させる方法です。金属積層造形では最も利用されている方式で、弊社で所有する金属3Dプリンターもこの造形方式になります。
そのほかに、・デポジション方式(DED:Direct Energy Deposition)金属などの材料粉末とレーザまたは電子ビームを造形部分に同時に照射し、溶融・積層して造形する方法
・バインダージェッティング方式(Binder Jetting)
金属粉末などにバインダー(液体結合剤)を噴射して選択的に造形する方法といった方式もあります。
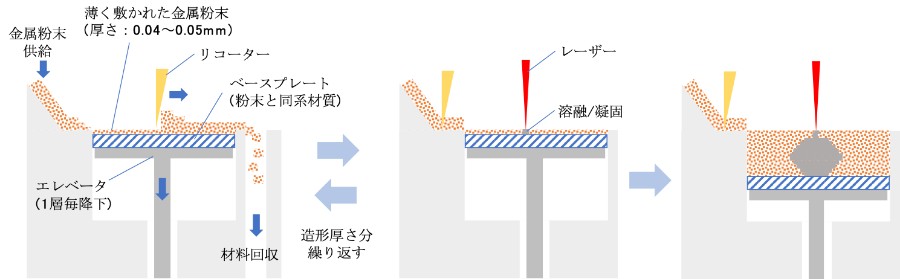
– 金属積層造形の制限について –
金属積層造形の原理は肉盛溶接に近い原理です。溶融した金属粉末の下に溶着できる部分があるかないかが重要となります。造形には独自のルールが存在し、部品の設計時に考慮することにより品質が向上する場合もある。
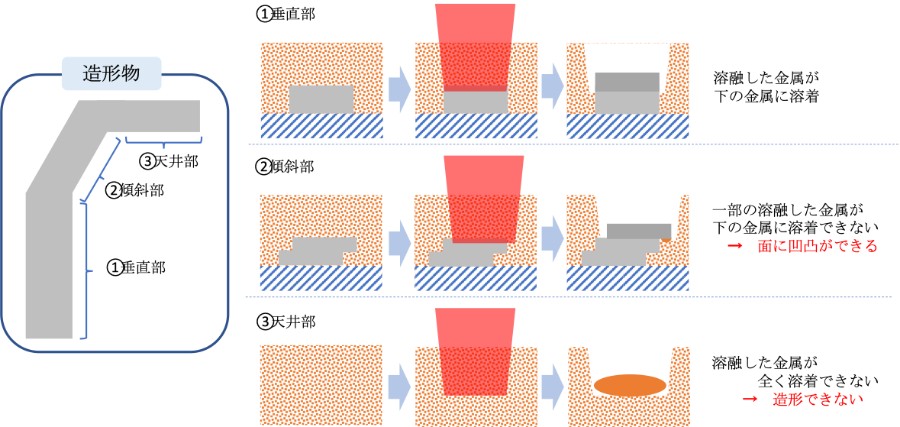
傾斜については、積層方向に45°程度が限界であり、それ以上寝ている形状はそのまま造形することができません。そのまま造形できない形状を造形するためには、サポートと呼ばれる支えを造形物と一緒に造形します。これらのサポートは、造形後に除去する必要があり、サポートの設置部は面の凹凸が発生します。そのため、コストの低減や、品質向上のためにも、設計段階で積層造形を考慮した、造形するときの向きを検討し、サポートを少なくすることが大切です。3D造形独特の現象を理解し、メリットを最大限に活かす設計をDfAM(Design for Additive Manufacturing)と呼びます。
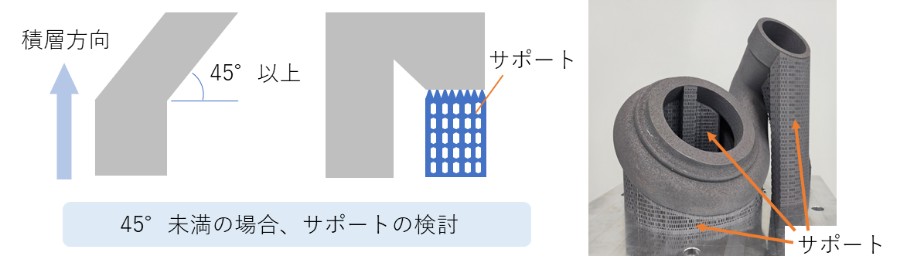
樹脂積層造形 -インクジェット方式(Material Jetting方式)
プレート上に紫外線を照射すると固まる特性を持つ光硬化性樹脂を1層毎インク状にして吹き付け、そこに紫外線を照射して固形化させることで立体を成型する方法です。インクジェット方式には造形材料にバインダー(結合剤)を噴霧して硬化させるBinder Jetting方式もありますが、当社ではMaterial Jetting方式の樹脂3Dプリンターを所有しています。家庭用の3Dプリンターとしても多く用いられる熱溶解積層法(FDM)などに比べて積層ピッチが小さく、滑らかな表面仕上げや、微細で複雑な造形物も作ることができます。
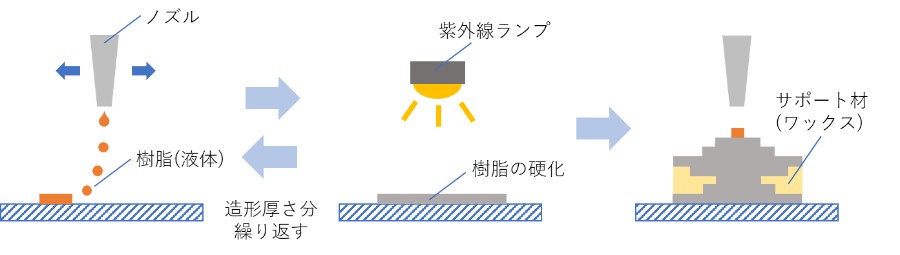
インクジェット方式の樹脂積層造形では、液体の噴射→紫外線硬化の手順を行うため、樹脂を乗せる箇所が必ず必要になります。そのため、必ずサポート材としてワックスを使用しながら製品の造形を行います。ワックスは低温(60℃程度)で液体になるため、造形後は恒温槽に入れて洗浄することで製品のみを取り出すことができます。金属積層造形のように複雑なサポート設計がないため、比較的簡単に製品を造形することが可能です。
一方で、サポート材による表面荒れが発生します。サポート材となるワックス、および硬化前の樹脂が液体であるため、硬化前は互いが混ざり合ってしまうことで表面の荒れの原因となります。
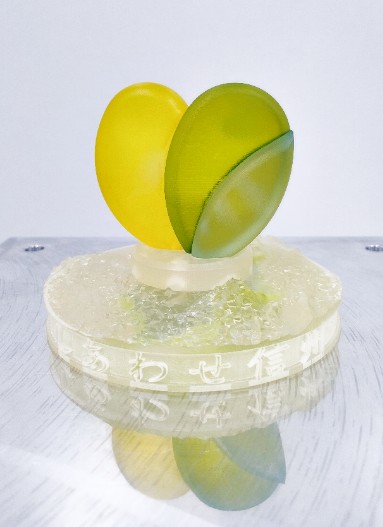